Erik Buffels: “ECO-Check is Topa’s response to the demand for sustainability among businesses”
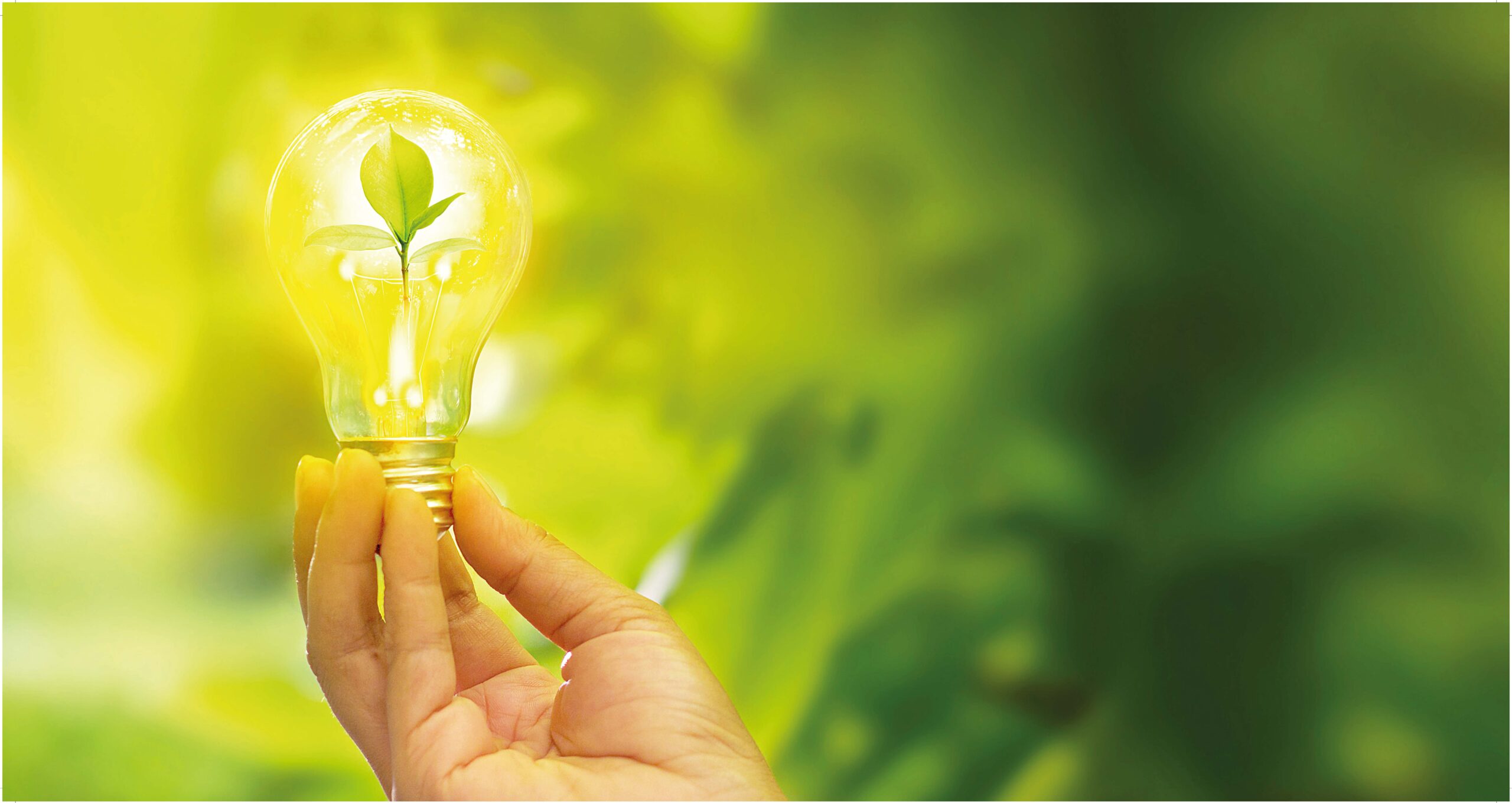
The Paris Climate Agreement states that we must limit the increase in the average world temperature by 2050 to well below 2 degrees Celsius, and ideally to 1.5 degrees Celsius.
Sustainability is a top priority. Every company must have a plan ready and have implemented it by 2050. ECO-Check is Topa’s response to the demand for sustainability among businesses.
Erik Buffels
“We are working together to consider how we can package products in an environmentally responsible way”
The Packaging Consultant developed the ECO-Check himself in 2019. Erik believes the name is logical, given everything that was happening and is still happening today: global warming, air pollution, soil contamination, flooding, plastic in the ocean, depletion of resources.
With the ECO-Check, we work together with businesses to consider how we can package their products in an environmentally responsible way.
Erik Buffels
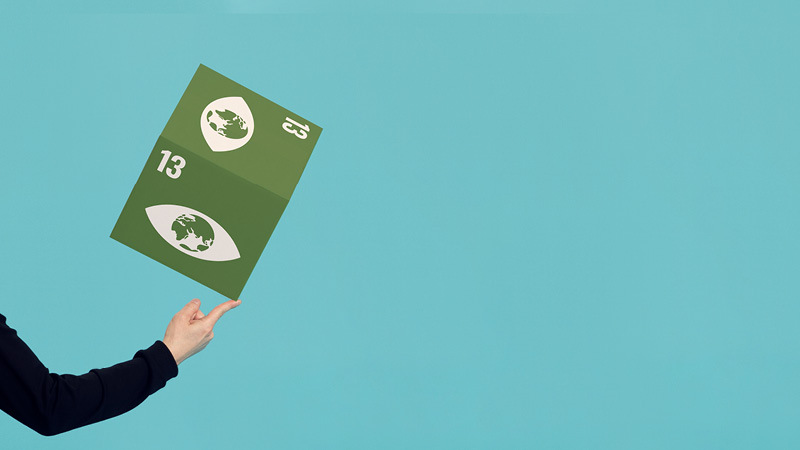
ECO-Check is about environment, economy, e-commerce and much more
Clients often turn to Topa to help them meet their SDGs or Sustainable Development Goals within their packaging process. But it goes much further than just the environment.
It’s about innovation, ease of use and ergonomics as well as sustainability. It’s about total cost of packaging and productivity. Because the packaging process needs to be economically responsible as well. It’s about image. Packaging also has to have the wow factor. And finally, ECO-check is about e-commerce and our e-commerce consultants.
Erik Buffels
“We’re invited to participate in the packaging process”
We sit down with the customer and look for ways to make improvements. We don’t just consider sustainability but definitely take costs into account too. We focus on the total cost of packaging and try to bring costs down. We are invited to participate in the packaging process. And you notice all kinds of things. You discover that pressing a button more than a hundred times a day has an impact on people. It results in injuries and eventually in sick leave. We then look for opportunities for improvement. That could be an ergonomic solution, but it could also mean automating that part of the packaging process. Another time you might discover that employees have to cover long distances. By organising the packaging process more efficiently, you can significantly increase productivity.
Erik Buffels
“The only problem is that online shops often haven’t given much thought to the packaging element”
Online shops often know exactly what they’re doing. The website works quickly and looks great. The products are displayed attractively with good descriptions. The online payment platform works perfectly. The only problem is that online shops often haven’t given much thought to the packaging element. We guide them through this process. We work closely with the business to choose the right packaging materials for the products. We draw out how the packaging process could work best, draw in packing tables, use roller conveyor systems where necessary and automate the process if desired. We ensure that whole process runs as smoothly as possible. Businesses often earn their investment back within just a couple of months.
Erik Buffels
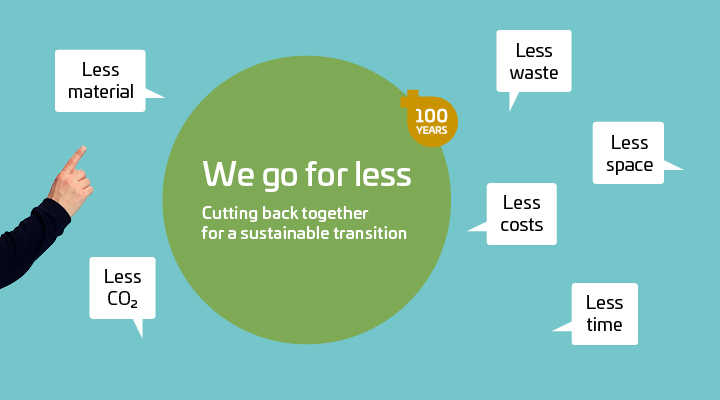
“With the new packaging, we can now fit four robot mowers into a container instead of one”
A company that exports robot mowers to America and Asia had a problem. With the existing packaging, it wasn’t possible to fit two robot mowers into the same sea container. The company could only ship one robot mower per container, which meant that the transport costs were extremely high. That’s when the company approached Topa.
We then set to work, along with the client. The process took several months. The designers and engineers at Topa Institute, our development, testing and research centre, were closely involved. And the results speak for themselves. We adjusted the packaging and tested it at the Topa Institute. So we could be sure the packaging would provide optimum protection of the product during storage and transportation. With the new packaging, we can now fit four robot mowers into a container instead of one.
Erik Buffels
“An expensive whisky’s reputation must of course be kept intact during transport”
Another great example is a company that transported expensive whiskies, worth between 300 and 800 euro per bottle.
The customer was very upset about bottles arriving with damage. An expensive whisky’s reputation must of course be kept intact during transportation. We developed an insert for this purpose, so that the bottles would no longer come into contact with the walls.
Erik Buffels
“Just like Topa, customers often also want to aim for less”
Companies want to make progress when it comes to sustainable business. Just like Topa, they often also want to aim for less. Our customers want to know what the most environmentally responsible packaging material is for their products. I recently had a customer who wanted to stop using foam. At his request, we creating a packaging solution made entirely from cardboard. Very environmentally friendly. Because then you only have one waste stream and you don’t have to separate them from one another anymore.
Erik Buffels
Aiming for less together, to achieve a sustainable transition
Less CO₂, less material, less waste, less time and less space. This is the aim in the packaging process. We love to help our customers achieve this. And the best bit is it often results in significant savings too.
Erik Buffels