Transport simulation
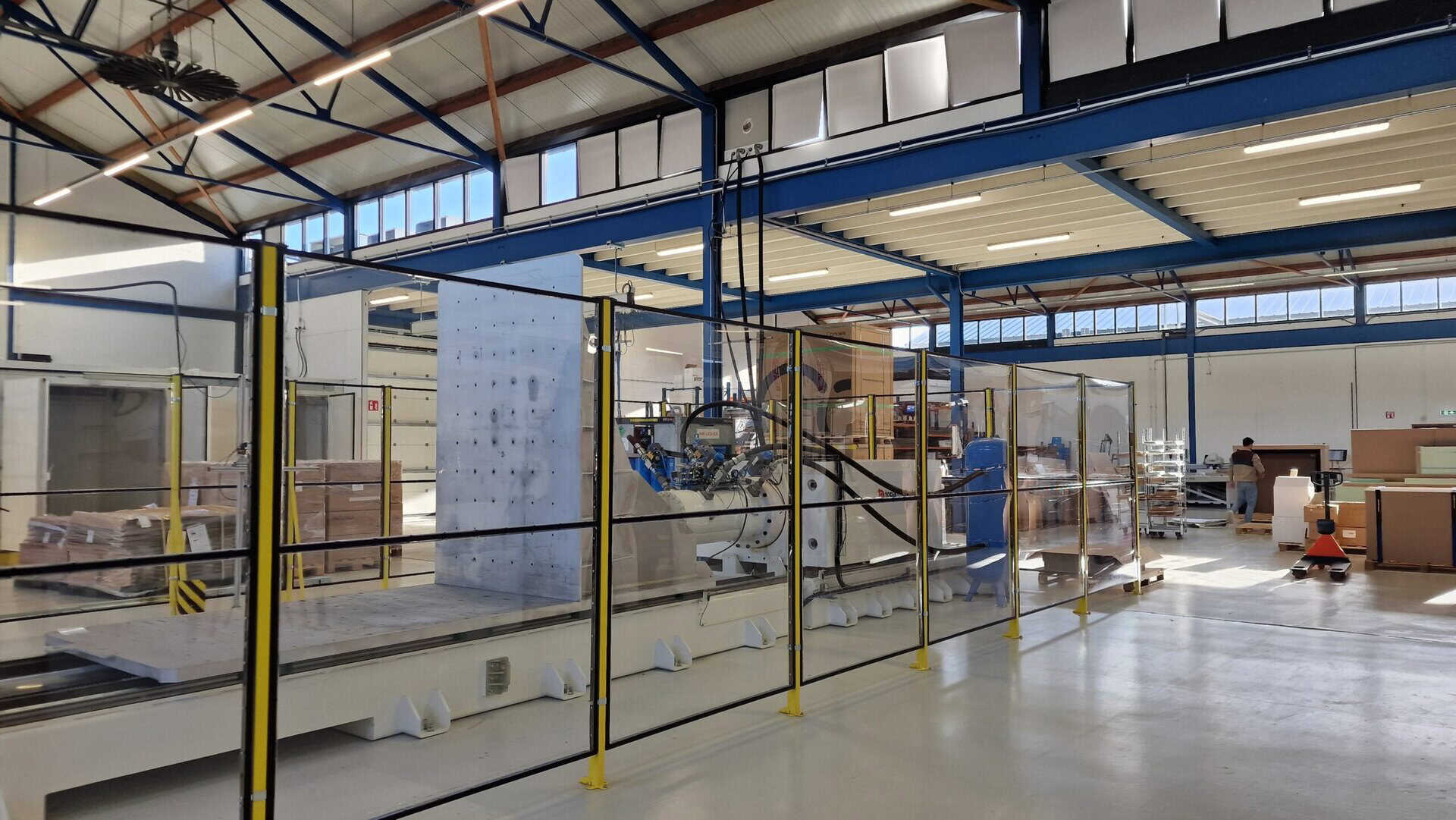
With mechanical transport simulation, we accurately replicate the forces your product and packaging may face during transport and storage.
We analyse the results and translate them into concrete improvements to your packaging, load securing, or product itself.
Tests are carried out according to international standards such as ISO, ISTA and ASTM – or customised to your own specifications. Our engineers actively help determine the best approach and, if needed, develop new test setups tailored to your needs.
While testing loose packages, various aspects are taken into account. After all, the package must be able to withstand falling (accidental dropping), vibrating (in the truck, on the conveyer belt, etc.), pressure (in the roll cage containers of other packages), and shocks. Besides, moist, heat, or condensation may also cause the packaging to weaken and the product to become more vulnerable. While setting up the test, the manner of transport, the weight of the package, and the fragility of the product are always taken into account.
Free fall drop test
What does falling do with the product or the packaging? Does it fall on the bottom, upside down, on the side, or on a corner? After each drop in a series of drops in conformity with the test standard, the consequences for the product are analyzed. This test is often conducted with multiple packaging solutions. In that case, various types of packaging are tested to acquire insight into whether a type of packaging might offer too little or too much protection.
Vibration tests
Whether your product is transported by truck, train, boat, or plane, vibrations always occur during transport. This is a strain on the product and the packaging, and they have to be able to withstand it. A random vibration test simulates this and reveals possible consequences for the product/packaging combination. In case of sudden potholes in the road (poor road surface) where the load may even come loose from the floor, the product/packaging combination should not break, either. These conditions are simulated by means of a loose load vibration test.
Strength determination of packaging
For all types and sizes of packaging, the strength may be determined by the compression test system. As soon as the packaging collapses during this test, the maximum compression value has been reached. This maximum value is not equal to the weight that can be placed on the packaging during transport and storage. Factors that strongly influence the packaging strength may by taken into account by using safety factors. Think of storage duration, environmental conditions (high humidity), and stacking height, for instance.
Concentrated impact test
For small cardboard packaging, made of a single wall, a concentrated impact test may be conducted. Through this test, it is investigated whether the packaging can withstand point-concentrated load.
When testing pallet loads, various influences must be taken into account. Pulling up and braking of the trucks, loading and unloading with a forklift, shunting of the train, turbulence during the flight, and so on. Moreover, moist and high or low temperatures can weaken the pallet load.
Horizontal shock test
The horizontal movements (sudden braking and shunting) of the pallet load affect the stability of the load. In order to ensure that the load remains on the pallet during transport, a horizontal shock test is performed. The impact speed is recorded in the test standard and 4 sides of the pallet are tested. This way, it is determined whether the pallet load is sufficiently stable on the pallet.
Compression and vibrations
During storage, packagings stacked on a pallet are static for a long period of time. Over this period, the products and packages will set. This may affect the compressive load on the bottom packaging and can even lead to loads falling over. This form of compression is also referred to as static compression. After this test, the strength of the total pallet load in a static situation is known. Another form of compression is dynamic compression. This type of compression occurs when the pallet load is in motion, for instance, during the ride on the truck. The compression strength must be larger in this situation, because the packagings also exercise pressure on each other during movement
Pallet drop test
During transport, pallet loads undergo small drops, for instance during the loading and unloading of containers on a ship. In order to know what this handling of a pallet does to your product, a pallet drop test is conducted. The pallet drop test can be conducted in various variations: flat drop, edge drop, or corner drop. Irrespective of the type of drop, the test is always conducted on 2 or 4 sides of the pallet. The drop height depends on the weight of the pallet load: more weight means a lower drop height.
Pallet performance tests
The use of pallets in a distribution environment is often considered to be normal. However, pallets must also meet certain requirements. Pallets are strained in different ways in different usage situations. Think of placement in a rack, stacking the pallet, lifting with a forklift, and the load of the product. By means of pallet performance tests (using the compression test system), the strength characteristics of pallets can be determined. This is true for wooden, plastic, as well as cardboard pallets
In order to determine the right packaging for your product, it is essential to know which influences your product can withstand. Topa Institute investigates the sensitivity of electronic products for shocks and vibrations. All products that are sensitive to climatic conditions are tested in the climate chambers.
Shocks
After dropping a laptop, for example, the outside does not necessarily show a lot of damage, but the laptop will no longer turn on; the critical G-value has been exceeded. Through a vertical shock test, it can be determined which G-value is critical to your product. The buffering packaging may be designed in correspondence with this value.
Vibrations
Especially for electronic products, a resonance test can help to determine at which frequencies parts of the product come in resonance and may eventually break due to vibrations. Low frequencies (< 50 Hz) often occur in transport. If your product responds to these frequencies, this will need to be considered during the design process of the packaging.
Climate
Is your product sensitive to high or low temperatures? Or can moist perhaps cause damage? By conducting a climate test, it can be tested at which temperature or humidity degree your product will no longer function properly and, therefore, against which conditions it has to be protected during transport.